Battery Management System
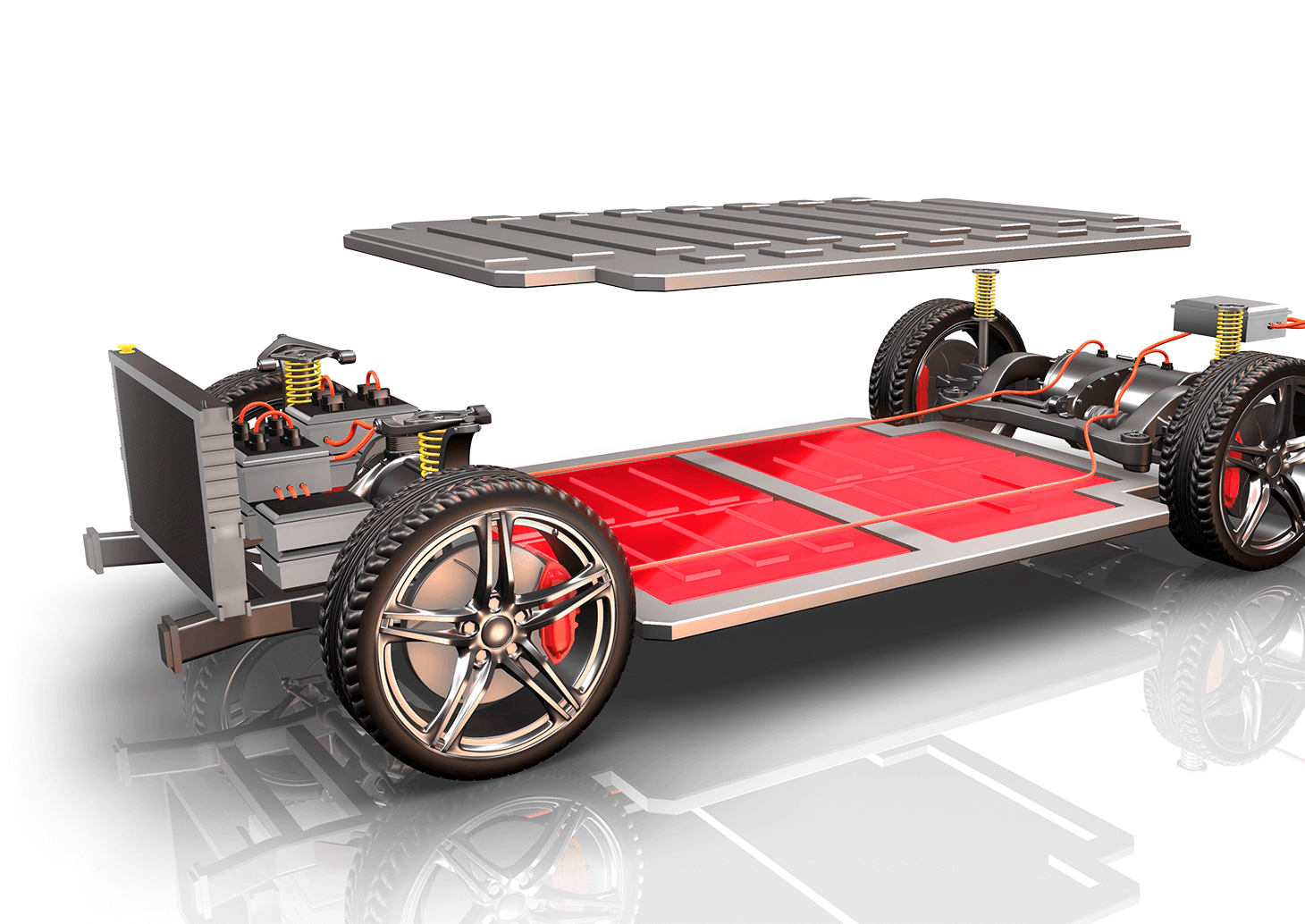
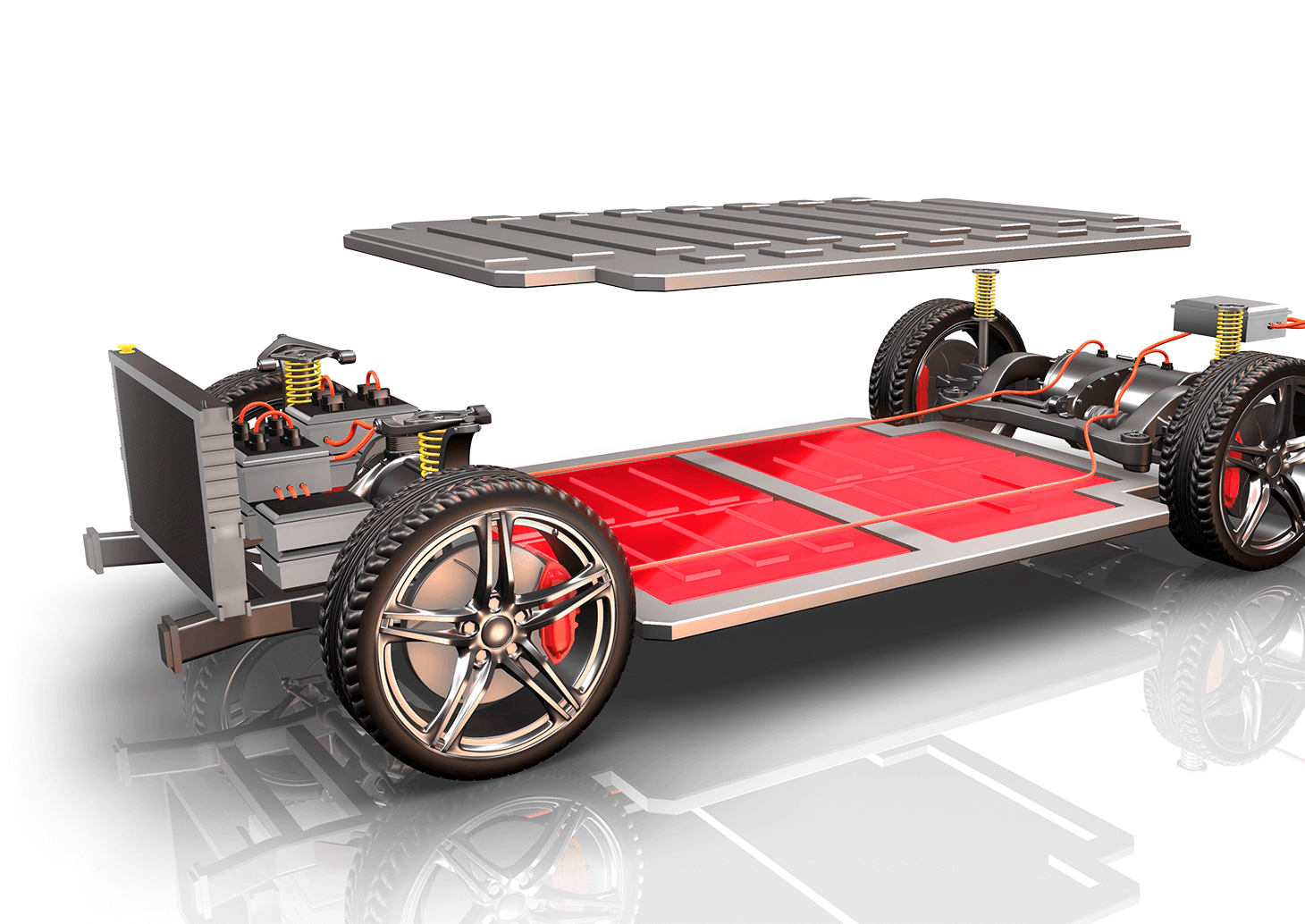
Optimize Your Battery Management with HIL.
Challenges in State-of-the-Art BMS Development
Developing a reliable BMS for EVs is challenging due to complex battery dynamics, temperature-dependent behavior, and variations in cell capacity and resistance. Ensuring accurate SoC and SoH estimation, maintaining thermal stability, and preventing faults like thermal runaway are critical concerns. Engineers must also test various battery chemistries while meeting strict safety and performance standards under real-world conditions. Typhoon HILās BMS HIL Testbed addresses these challenges with real-time simulation and a Smart Cell Emulator for precise cell behavior replication and fault testing. Its scalable design supports different battery chemistries and voltage ranges. This solution accelerates development while ensuring safe and efficient BMS validation.
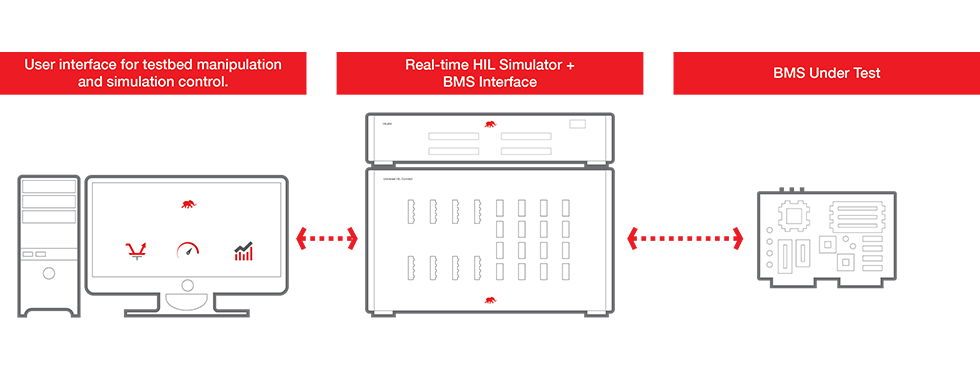
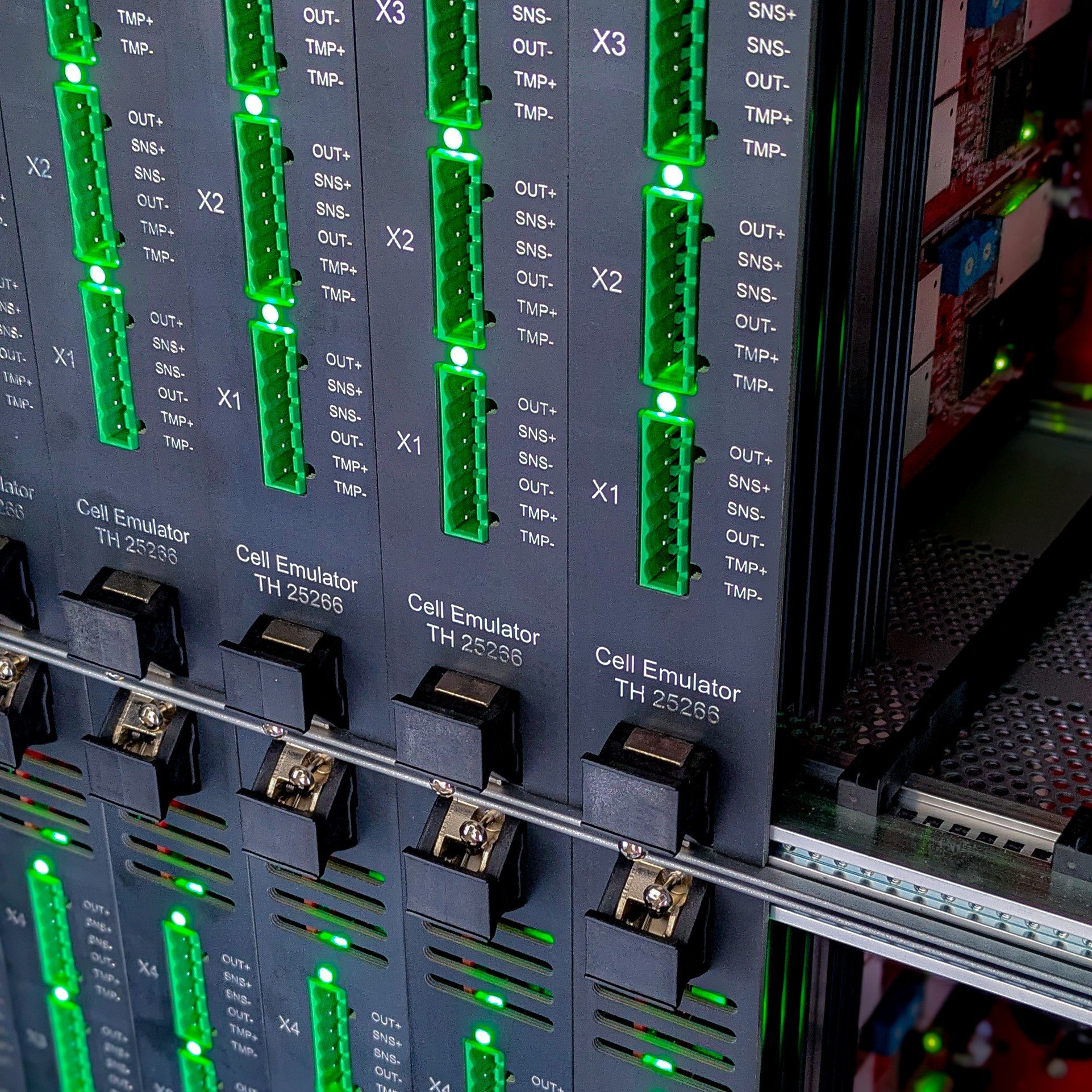
Scalable Testing Platform
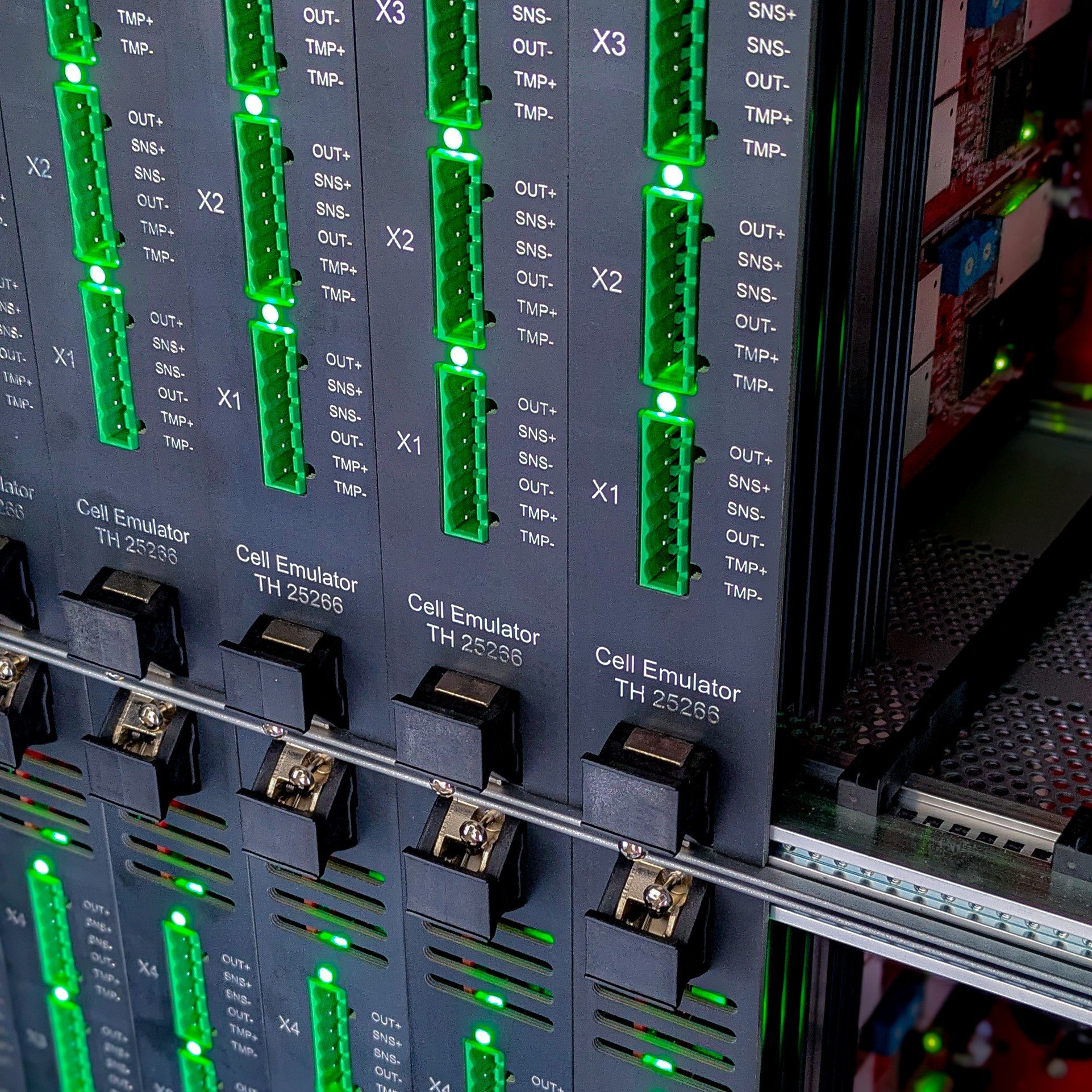
Different e-Mobility applications require varying battery capacities and voltage levels. Electric scooters and bikes use 48V to 72V systems, passenger EVs range from 300V to 800V, and electric trucks and buses exceed 1000V for higher power needs. These differences demand adaptable BMS solutions to optimize performance across applications. Typhoon HIL solutions offer support for systems from 16 cells to 256 cells.
Integrated Solutions Provider
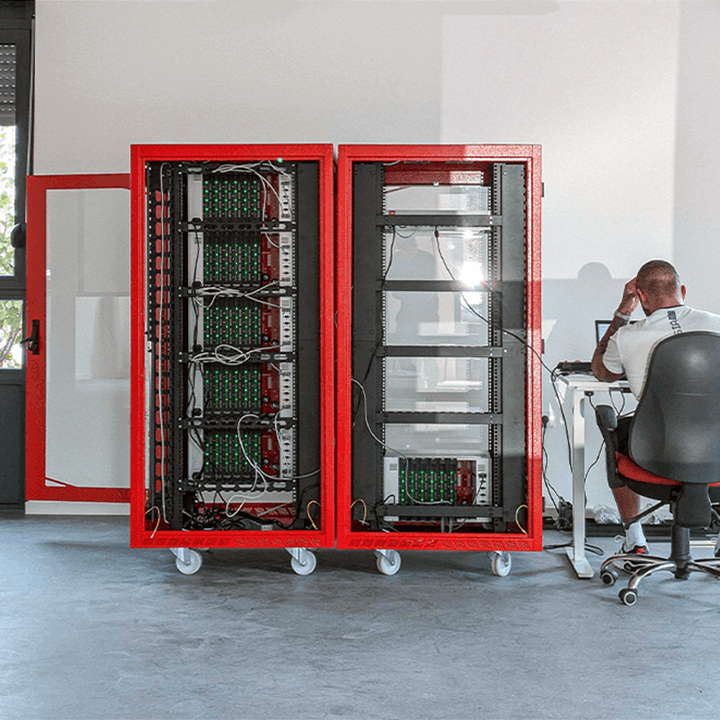
Multi-vendor solutions can create challenges in BMS testing, such as integration issues and inconsistent performance across different platforms. Typhoon HIL addresses these challenges with a fully integrated solution, combining real-time simulation, precise cell emulation, and fault testing. This streamlined approach allows engineers to validate BMS strategies safely and efficiently, reducing development time while ensuring safety and performance. With the ability to simulate diverse battery behaviors, Typhoon HIL accelerates innovation and supports the rapid deployment of high-performing BMS solutions across various e-Mobility applications.
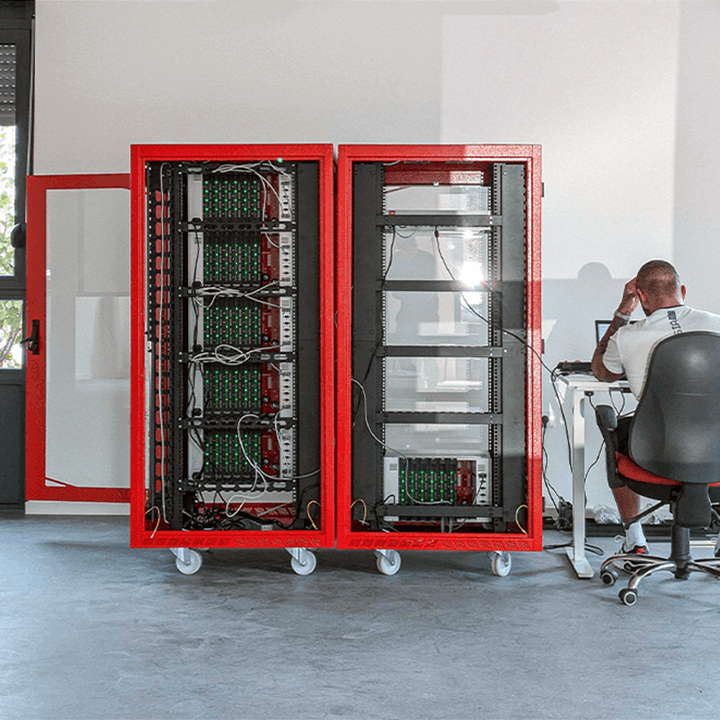