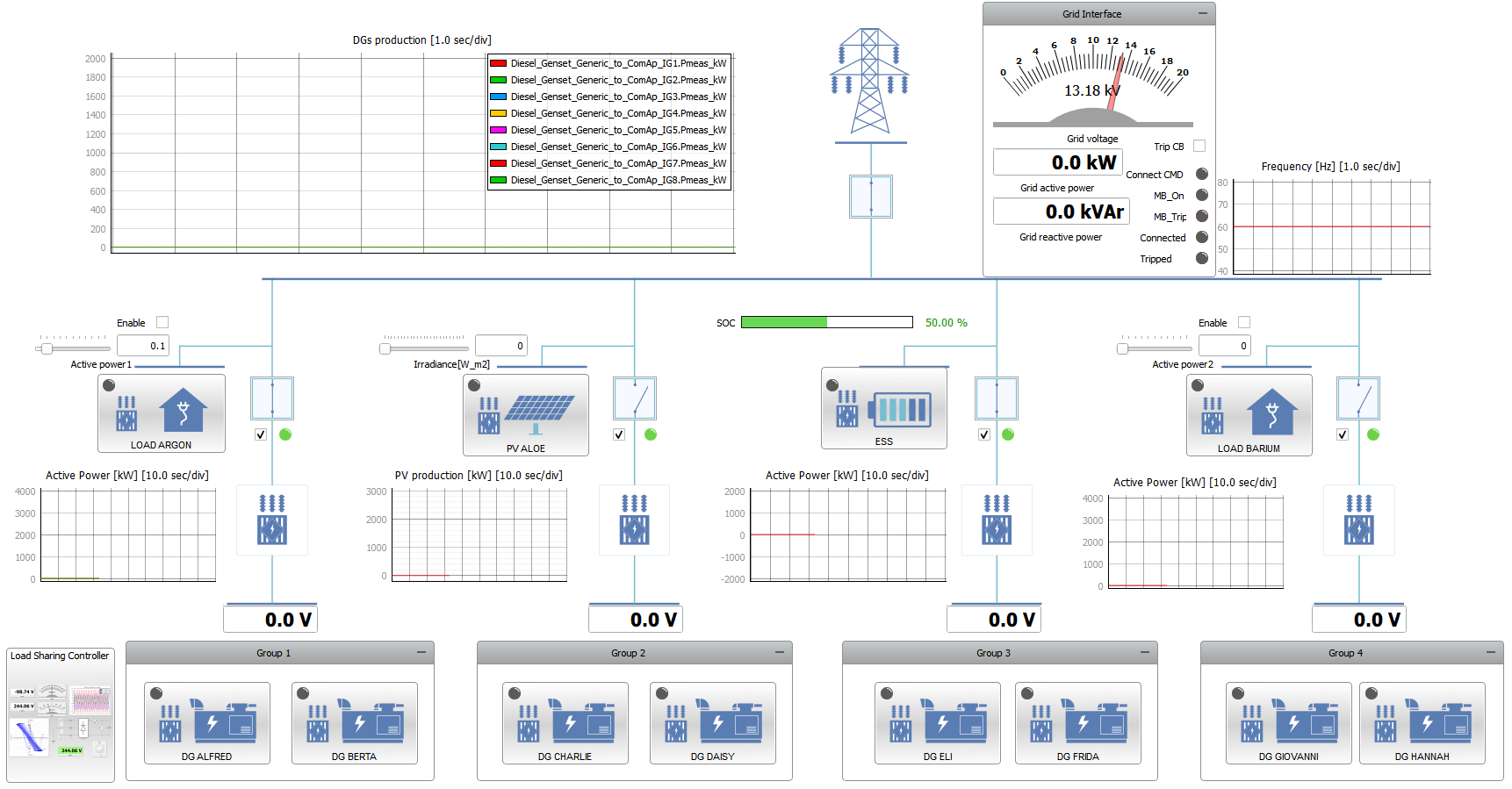
Initially, Rolls Royce carried out microgrid integration testing at a demonstration facility. A prototype battery system, a genset, and other items of equipment allowed quick results to be gathered. With around 50 running microgrids in the field, a growing customer base, and increasing complexity, testing at the demonstration facility became impractical. The alternative option, testing in the field, carried too much risk for the customer. As such, Rolls Royce sought a better solution to ensure equipment was correctly integrated and the control system worked as expected, and HIL fit the bill.

As system integrators, Rolls Royce takes off-the-shelf items of equipment and brings them together to make an AC coupled battery storage system. This is then integrated with the whole microgrid, and Rolls Royce ensures all the different parts work together.
Documentation is only a start when you work with these components. You always learn something new in the field.
David Dunnett
Head of Software Development
Rolls Royce
Using HIL testing allows Rolls Royce to reduce surprises in the field, making commissioning easier and faster. With customers in Indonesia, Haiti, and Greenland, to name a few locations, reducing surprises also helps to cut travel time and cost for engineers and technicians.
We have a long list of existing energy equipment that we can already talk to, control and support, but every time we add a new one, you’re adding uncertainty and risk. We want to make sure that everything is still working as it did before.
David Dunnett
Head of Software Development
Rolls Royce
Real-time simulations of components, coupled with the actual controller, create a mock interface for running a variety of test cases. This allows Rolls Royce to carry out regression testing of the control software, providing confidence that updates can be deployed on older systems, and new features can be added without breaking old ones.
Subscribe to blog updates in the top right
to be the first to receive the upcoming blogs by email.
Additional information: The full Special Report was originally published with Microgrid Knowledge as a 6-part series. You may follow the links to read the original publications on their website:
- Hardware in the Loop: Addressing the Challenges of Microgrid Systems Integration
- How to Validate a Microgrid Project
- Pros and Cons of Testing Methods to Validate Microgrid Designs
- How Hardware in the Loop Tests the Functionality of Microgrid Controllers
- Streamlining Microgrid Development with Model-Based Engineering
- How Does Hardware In the Loop Work in the Real World