Introduction | Revolutionizing Power Management in Hybrid Mining Trucks
In the mining sector, the operational efficiency of large vehicles is essential for competitiveness and sustainability. Mining trucks, such as those used by U&M Mineração e Construção, consume substantial fuel and contribute significantly to emissions and maintenance costs. To address these challenges, integrating innovative technologies that improve energy efficiency, reliability, and reduce emissions is crucial.
A promising solution is the integration of electrical storage systems in mining trucks. This technology harnesses braking energy that would otherwise be wasted, storing and reusing it for vehicle propulsion. This not only reduces fuel consumption but also lowers emissions and the wear on the internal combustion generator, leading to more sustainable and cost-effective operations.
One notable example of this approach is the Komatsu 730E, a 186-ton mining truck used by U&M Mineração e Construção. Originally, the Komatsu 730E does not have a battery system; however, the current project aims to integrate a battery into the vehicle. This integration will allow the truck to regenerate braking energy instead of dissipating it through a grid of resistors. To manage this complex system efficiently, a 1.2 MW DC-DC converter was designed. This blog explores the role of Typhoon Hardware-in-the-Loop (HIL) systems in the development of this converter, enhancing both reliability and performance.
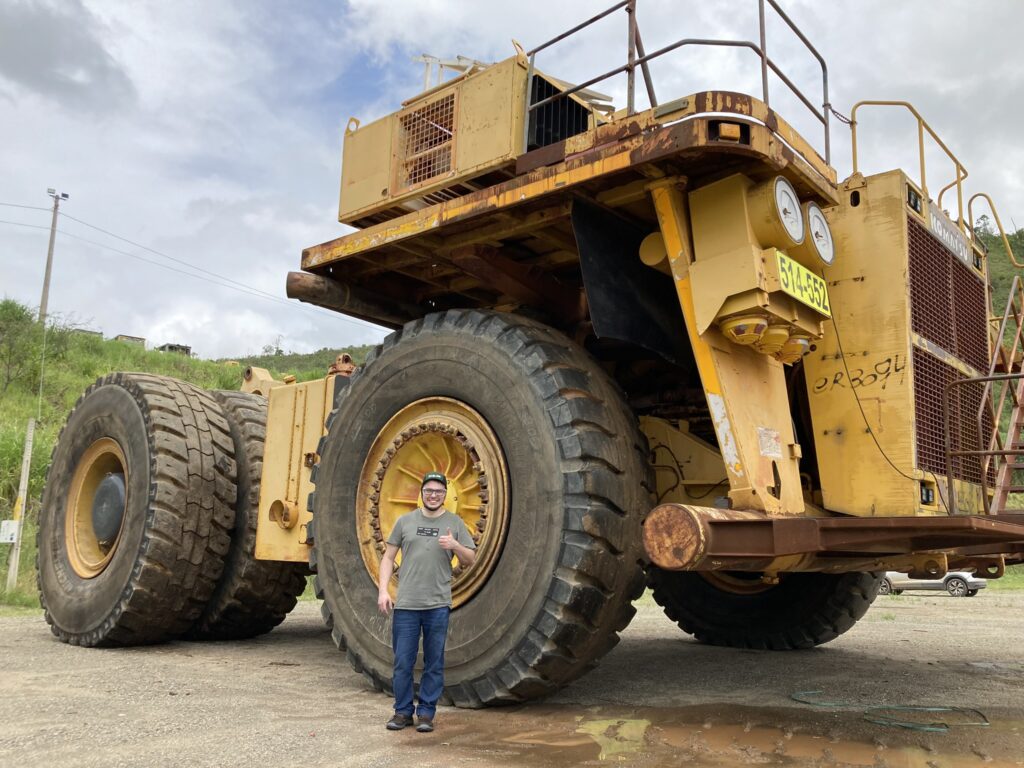
Challenges | Hybrid mining truck 1.2 MW DC-DC validation
Developing a high-power DC-DC converter for the Komatsu 730E presents several challenges. Operating such a massive vehicle incurs high costs, both in terms of fuel consumption and space requirements. The converter must handle substantial power levels while maintaining efficiency and reliability under harsh operating conditions. Additionally, working with high-power systems carries significant risks, any failure could result in catastrophic damage to equipment and pose serious risks to personnel safety. Traditional testing methods often fall short of providing the necessary insights and flexibility required for such a complex task. Engineers need a robust and flexible testing environment to simulate real-world conditions accurately and identify potential issues early in the development process.
Solution | Typhoon HIL for advanced simulation and testing
To validate the project, Typhoon HIL was used, enabling detailed analysis of the converter’s operation under various conditions. This simulation process was essential for ensuring the harmonious operation of all components and optimizing system development.
The project setup included an Interface board between the control board and Typhoon HIL. In this configuration, digital signals generated by the control board are sent to the HIL as digital inputs for the simulated IGBTs. Simultaneously, analog signals resulting from current and voltage measurements across simulated components are scaled to emulate real-world signals in both amplitude and connection type (differential or single-ended). These analog signals are then fed back to the control board, where they are processed by the control algorithm and are recalculated into digital signals for the IGBT and the cycle continues.
A complete simulation of the entire system was performed, starting with the battery pack, contactors, and DC-DC converter, extending to emulate the dynamics of the truck. This includes a DC electric motor supplying torque to a model corresponding to the dynamics of the truck, considering factors such as aerodynamic drag, inertia, and gear ratio. These factors are used to calculate and return the mechanical speed to the DC machine, allowing detailed observation of the real dynamics of the vehicle with respect to a control reference.
The Typhoon HIL also supports CANopen network emulation. Using the files provided by the manufacturer, it was possible to emulate the communication between the converter and the IGBT modules. This was essential to understand the module communication and prepare the communication functions. After validation through simulation, bench tests were conducted to verify the operation of circuits, converters, and cabling. Finally, the system was tested in real-world applications, evaluating the performance of the design under operational conditions.
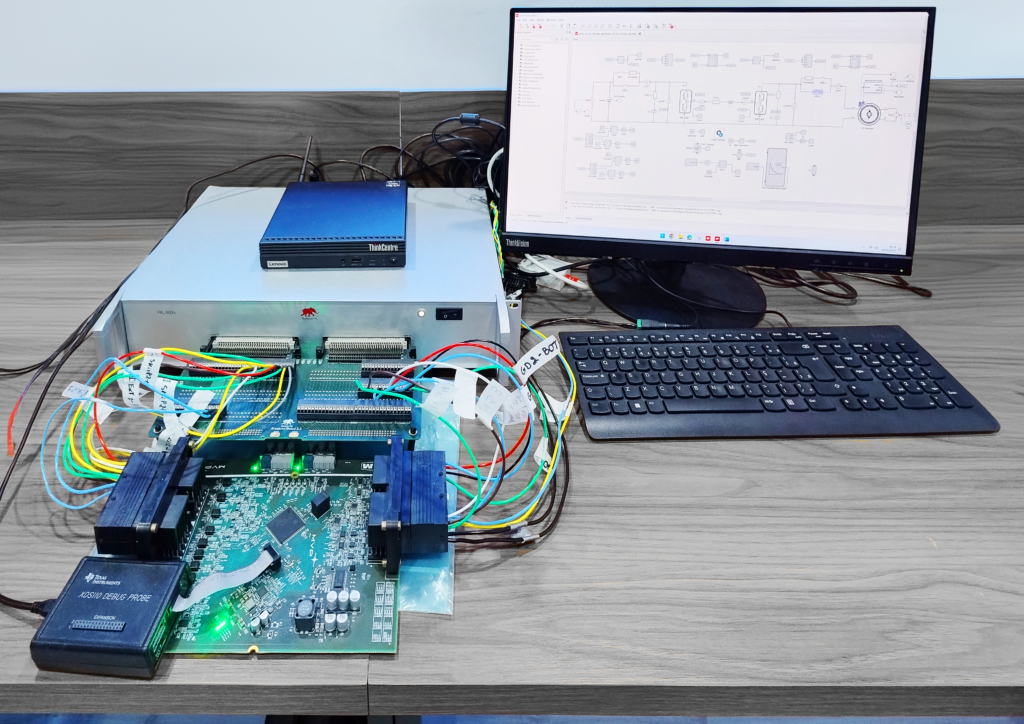
HIL Benefits | Improving efficiency, reliability and cost-effectiveness
The benefits of using Typhoon HIL for developing a 1.2 MW DC-DC converter for the Komatsu 730E are substantial:
- Risk Reduction: By simulating real-world conditions, engineers can identify and mitigate potential issues early in the development process, reducing the risk of costly failures in the field.
- Cost Efficiency: HIL simulation allows for extensive testing without the need for multiple physical prototypes, significantly lowering development costs.
- Time Savings: The ability to test and validate designs in a virtual environment accelerates the development cycle, enabling faster time-to-market for new technologies.
- Enhanced Reliability: Comprehensive testing ensures that the final product is robust and reliable, capable of performing under the demanding conditions of mining operations.
- Flexibility: Typhoon HIL systems provide the flexibility to test various scenarios and configurations, ensuring that the DC-DC converter can handle diverse operational demands.
In conclusion, the use of Typhoon HIL systems in the development of a 1.2 MW DC-DC converter for the Komatsu 730E hybrid mining truck represents a significant advancement in engineering practices. By leveraging the power of HIL simulation, engineers can create more efficient, reliable, and cost-effective solutions for the mining industry, paving the way for more sustainable and efficient operations.
Credits
Authors | Thiago Motta, Hermano Campos
Visuals | Hermano Campos
Technical Editor | Thiago Motta
Blog Editor | Debora Santo