Introduction | New technologies, new opportunities
Rapid advances in CMOS (Complementary Metal Oxide Semiconductor) detectors open new possibilities for X-ray based diagnostic imaging. Imaging software can now extract vast amount of information hidden within signals coming from the detectors. Systems for general radiography can be optimized for specific tasks, such as detection of COPD (Chronic Obstructive Pulmonary Disease) and the resulting 3D image quality is on par with images from CT scanners of just a few years ago. Cost of such a system is a fraction of a CT scannerās cost.
A high-quality imaging starts with the source: to get the best out of what detectors and software can do, an X-ray generator needs to be fully integrated with the system: it must have a two-way communication with other parts of the imaging chain, and it must power, control and protect an X-ray tube. To meet the challenges, new power electronics technologies must be used and a new approach to development of such a complex product is warranted.
Challenges | Developing an X-ray generator for tomorrow
New generations of CMOS detectors make it possible to use fluoroscopy with high frame rates: 30 frames per second (FPS) is the standard in new equipment, 60 FPS is coming soon, and 90 FPS is on the horizon. Other imaging techniques, like serial radiography, tomography, and CINE imaging, follow the suit. Such a high-rate imaging requires synchronized X-ray pulses, which means that high voltage powering X-ray tubes must go on and off very quickly. It is crucial that the rise and fall times of the high voltage are short, for two reasons: (1) to minimize low-dose radiation to the patient which does not contribute to the image and (2) to allow sufficient time for proper reset of the CMOS detector.
In addition to the high-speed pulsing, it is desirable to achieve maximum set voltage without overshoot or ringing at the top of the waveform. Also, it is important to achieve high pulse-to-pulse repeatability, which is crucial to getting high quality images. Every generator needs to work with various X-ray tubes, and the tubes are very non-linear loads. The same power quality is required for wide range of operating conditions, accommodating various patient anatomies.
The above is where the classic analog control falls short: it is impossible to optimize feedback loop parameters for many different combinations of voltage and current output and such solutions are compromises that set limits on the overall system performance.
An on-the-fly adaptable control system is the approach that removes obstacles to high-performing radiographic systems.
Solution | āFull-digitalā to the rescue
To meet the challenges, a fully digitally controlled high voltage power supply for X-ray generators is being developed by Advanced High Voltage. The control system is based on a latest generation DSP (Digital Signal Processor). This opens possibilities for optimizing feedback loop compensation for every calibrated operating point (14-30 settings, depending on a system and X-ray tube) and to interpolate parameters for other settings.
A simulation software optimized for power electronics circuits, coupled with years of practical experience, is used to determine a starting set of the loop compensation parameters. However, simulation can only get us so far, and the proof is in the pudding, as the saying goes. In our case āthe puddingā is a control board with all the required interfaces and a HIL404 real-time simulation device, which is playing a role of the high voltage power stage with an X-ray tube connected to it. The control board processes system inputs, generates PWM MOSFET drive signals and filament current reference, which are sent to the HIL device. The HIL404 emulates the high voltage power stage loaded with a non-linear X-ray tube, and it sends voltage and current feedback corresponding to the PWM and filament reference inputs. In addition to the basic operation, critical faults are also returned by the HIL.
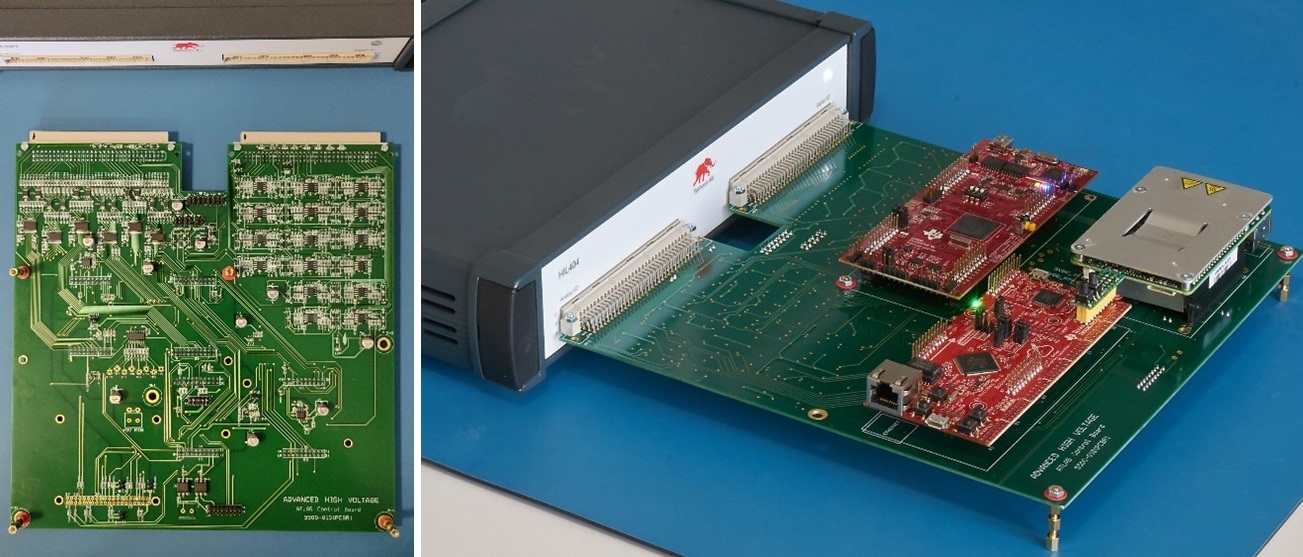
All important functions are available on the virtual control panel in HIL SCADA and the oscilloscope view gives a critical insight into the operation of the high voltage inverter. The high voltage and filament controls are directly accessible, and faults can easily be emulated.
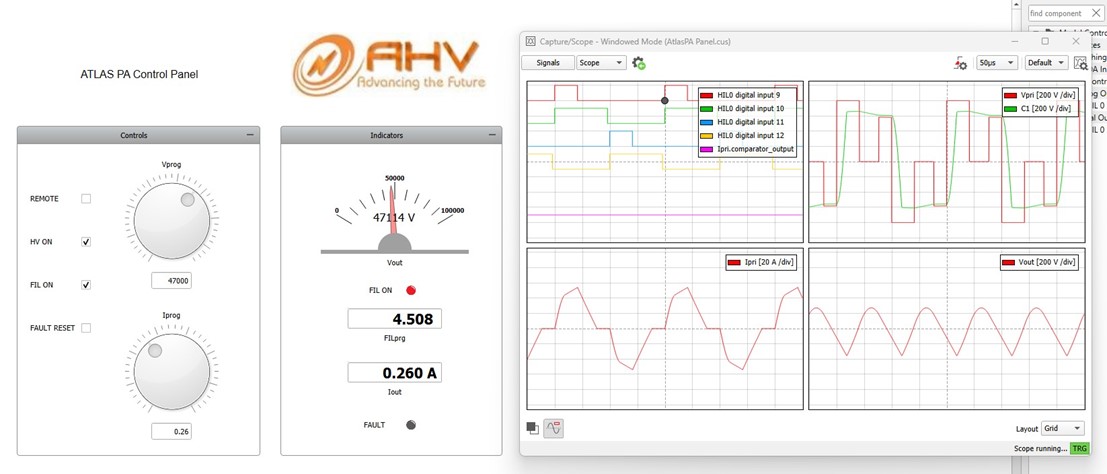
From a software and firmware development perspective, the control board sees the HIL device as a high voltage generator loaded with an X-ray tube of choice.
HIL Benefits | HIL saves time and money
The most valuable benefits of the HIL-based X-ray generator development can be summarized as follows:
- Simultaneous work on:
- Digital control algorithms,
- Generator firmware development,
- Software and GUI development,
- Hardware interfaces and power train development;
- A major part of the generator development and system integration can be done without using an actual X-ray tube, therefore there is no need for lead-rooms, radiation protection, etc. The work can be done in an office environment where the whole system fits on top of a desk;
- Easy integration of additional X-ray tubes, most of the work can be done based on the tube specifications;
- Enhanced collaboration: the development tasks can be distributed between teams in different locations;
- Early customer involvement: the customers’ developers can work on system integration in parallel with the generator development team;
- Troubleshooting production and customer service issues can be done remotely;
- Customerās setups can be replicated quickly for help during system deployment.
Integrating HIL into engineering processes makes it possible to develop high end radiographic generators of tomorrow. The new approach reduces time-to-market and improves collaboration between generator manufacturers and system integrators. The end result are systems with high level diagnostic imaging capabilities, giving radiologists tools for high quality care of their patients.
Credits
Text | Boris Sasic
Visuals | Boris Sasic
Editor | Debora Santo