Introduction | Why BMS Testing is Vital for EVs
The battery management system (BMS) plays a critical role in battery-dependent systems, such as electric vehicles (EVs) and energy storage systems (ESS). Its primary function is to monitor the battery’s state of charge (SOC) and state of health (SOH), collecting data on voltage, current, and temperature. By utilizing this information, the BMS ensures efficient and safe battery usage through monitoring, protection, management, and lifespan optimization. Since batteries are expensive, intricate, and delicate components, the proper functioning of the BMS is vital to e-Mobility applications.
Any failure in the BMS can lead to severe consequences, including safety hazards, reduced battery life, and compromised performance. Consequently, manufacturers must conduct thorough testing and validation of the software in their products. Ensuring compliance with regulations before the implementation in commercial products or systems is a real challenge to the e-Mobility industry.
Validation | BMS Algorithm Responsibilities
The BMS employs balancing algorithms to prevent uneven charging and maintain voltage stability in battery cells. Additionally, it accurately estimates SOC to avoid exceeding limits and works with converter controllers to protect battery cells against overcurrent and deep discharge. Failure of these algorithms can compromise the health and performance of the battery cells.
As the battery is the central piece of EVs, BMS algorithms must constantly communicate with other components, such as the control unit, charging station, and motor controller. Therefore, effective communication and protocol adherence is crucial for ensuring interoperability and exchanging accurate information.
Regarding security, the BMS is responsible for detecting and managing short circuits and cable failures. Therefore, it is constantly monitoring isolation between battery components. Furthermore, the BMS manages battery temperature, adjusting charging and discharging processes in response to overheating and preventing thermal runaway.
Challenges | Challenges in BMS Testing
The BMS incorporates numerous functionalities, as mentioned previously. Because of this, its testing process must encompass a wide range of operational scenarios to ensure the safe operation of EVs. As a consequence, companies invest substantial time and resources in meeting all the established test standards and requirements.
The primary challenge in testing the BMS lies in the number of battery charging and discharging cycles. This process demands significant energy and time since estimation algorithms rely on historical operational data to train machine learning models. Moreover, validating the optimal performance of BMS under diverse operating conditions is crucial for ensuring efficiency, which further increases the required charging cycles.
Another challenge arises when testing the BMS failure detection and management capabilities, particularly due to security concerns. Given that EV batteries are high-energy-density devices operating at elevated voltages, testing failures can be dangerous and costly, necessitating the availability of suitable infrastructure for efficient execution.
At the single-cell level, acquiring accurate information about the operation of each cell poses an additional obstacle when using real batteries for testing. Measuring cell voltage and temperature individually is impractical, leaving external measurements as the only viable option. Consequently, testing the BMS performance for different battery configurations becomes challenging and ineffective.
In addition to the control and monitoring functionalities, testing the BMS communication system also presents challenges. As the BMS interfaces with numerous devices, testing must ensure its correct utilization of standard communication protocols. However, with the emergence of bidirectional and wireless charging, as well as frequent updates to communication standards, the requirements and frequency of BMS communication testing have increased.
HIL Benefits | Improving BMS Testing with HIL
Model-based testing offers an alternative approach to testing with real batteries. However, in this case, it is essential to accurately emulate the behavior of individual battery cells, considering voltage levels and achieving precise control of voltage changes without overshooting. Otherwise, the validation of BMS algorithms will not yield meaningful results. Therefore, the reliability of test outcomes and the effectiveness of BMS performance validation highly depends on the precision of the cell and battery models.
HIL solutions, such as Typhoon HIL tools, provide a precise method to replicate the electrical and performance characteristics of battery cells. This enables accelerated development and validation of the BMS through accurate simulations, leading to cost savings. Since batteries are emulated, energy costs are significantly reduced, and tests can be conducted in parallel if sufficient computational power is available. Moreover, HIL solutions create a safe environment to test the BMS’s response to faults and evaluate its ability to protect the battery.
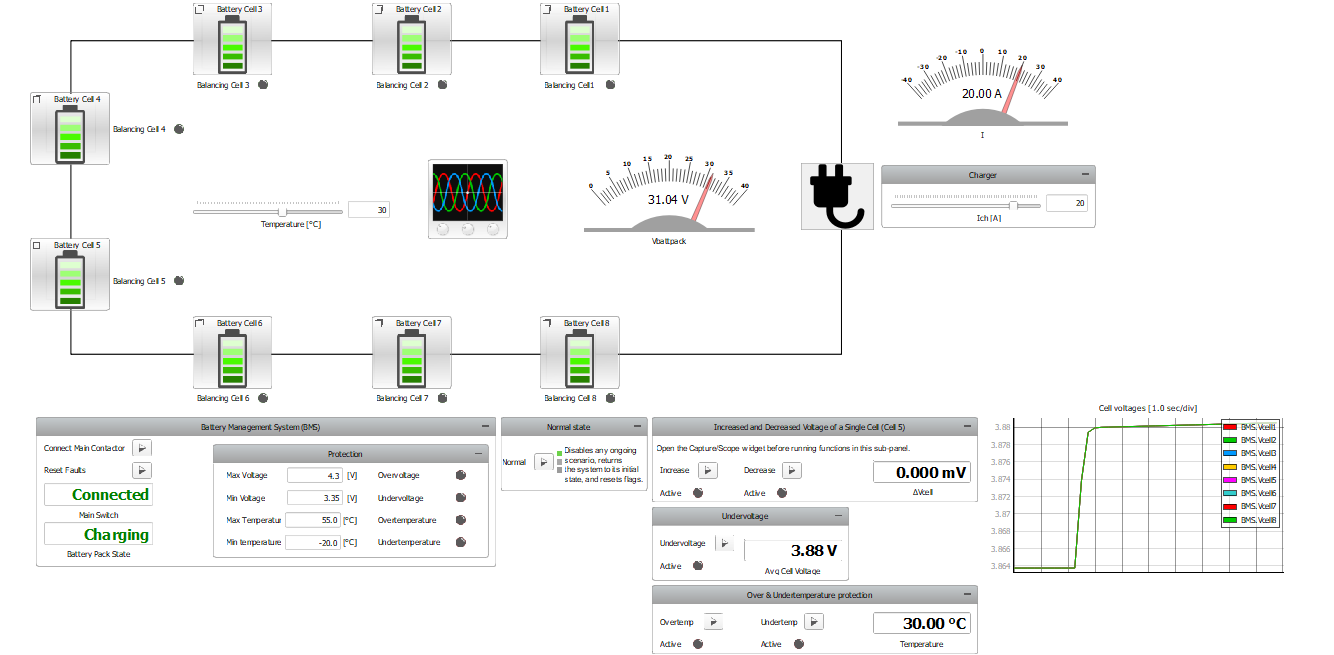
By employing virtual models for the battery, real-time simulation of various scenarios and operating conditions becomes possible. The digital twinning approach facilitated by HIL enables this capability. Leveraging the computational power of the cloud enhances the efficiency of BMS validation, incorporating historical data and accurate battery models.
Credits
Authors | Cassiano F. Moraes, Heitor J. Tessaro
Visuals | Karl Mickei
Technical Editor | Igor Pintaric
Blog Editor | Debora Santo